PP管材質管生產過程特性與變形控制
PP管材質管生產過程***性與變形控制
在現代工業生產中,PP管以其***異的化學穩定性、耐腐蝕性、環保性能以及相對合理的成本,在建筑給排水、化工流體輸送、農業灌溉等諸多***域得到了廣泛應用。然而,要生產出高質量的PP管材,深入理解其生產過程***性并有效控制變形至關重要。
一、PP管材質管生產過程***性
(一)原料***性
PP(聚丙烯)作為一種熱塑性塑料,具有******的分子結構。其分子鏈呈線型排列,這使得它在受熱時具有一定的可塑性。從物理性質來看,PP原料外觀通常為白色顆粒狀,具有******的流動性,便于在擠出過程中均勻地進入擠出機料筒。在化學性質方面,PP對多數酸、堿等化學物質具有出色的耐受性,這決定了PP管材在復雜化學環境下的穩定應用潛力。但同時,PP的分子結構也導致其在加工過程中對溫度、剪切力等條件較為敏感,微小的工藝參數變化都可能影響***終管材的質量。
(二)擠出成型過程
1. 塑化階段
擠出成型是PP管材生產的核心環節。***先,PP原料被加入擠出機料筒,隨著料筒加熱,原料逐漸受熱塑化。在這個過程中,溫度的控制至關重要。一般料筒溫度需***控制在***定范圍內,通常在180℃ - 220℃之間,具體溫度根據PP的牌號、配方以及所需的管材性能有所調整。如果溫度過低,原料塑化不完全,會導致管材表面粗糙、內部存在生料顆粒等缺陷;而溫度過高,則可能使PP分子鏈過度降解,降低管材的機械性能,如強度、韌性下降。
2. 擠出成型階段
經過充分塑化的PP熔體在螺桿的推動下,通過模具擠出成型。模具的設計直接決定了管材的初始形狀和尺寸精度。在擠出過程中,熔體受到一定的壓力和剪切力作用。合適的剪切力有助于PP熔體的均勻性和流動性,使其能夠順利地形成管材形狀。但過高的剪切力會產生過多的熱量,不僅可能損傷PP分子結構,還可能導致熔體黏度異常變化,影響管材的壁厚均勻性和外觀質量。此時,螺桿轉速與牽引速度的匹配尤為關鍵。螺桿轉速決定了熔體的擠出量,而牽引速度則影響著管材的成型速度和尺寸穩定性。兩者需要保持恰當的比例,以確保管材在離開模具后能夠平穩地冷卻定型,避免出現拉伸變形或壓縮變形。
(三)冷卻定型過程
擠出成型后的PP管材處于高溫軟化狀態,需要迅速進行冷卻定型。冷卻方式通常采用水冷或風冷。水冷具有冷卻速度快、效率高的***點,能夠使管材在短時間內固化,保持其形狀精度。但在水冷過程中,要注意水溫的控制以及冷卻水的均勻性,避免因局部冷卻過快或過慢而產生應力集中,導致管材變形或開裂。風冷則相對溫和,適用于一些對冷卻速度要求不高或***殊結構的管材冷卻。在冷卻過程中,管材內部的熱量逐漸向外傳遞,由于PP的導熱性相對較差,內外層的冷卻速度差異可能會引起管材的收縮不均勻,進而產生變形。因此,合理設計冷卻系統,確保管材各部分冷卻均勻,是保證管材質量的重要環節。
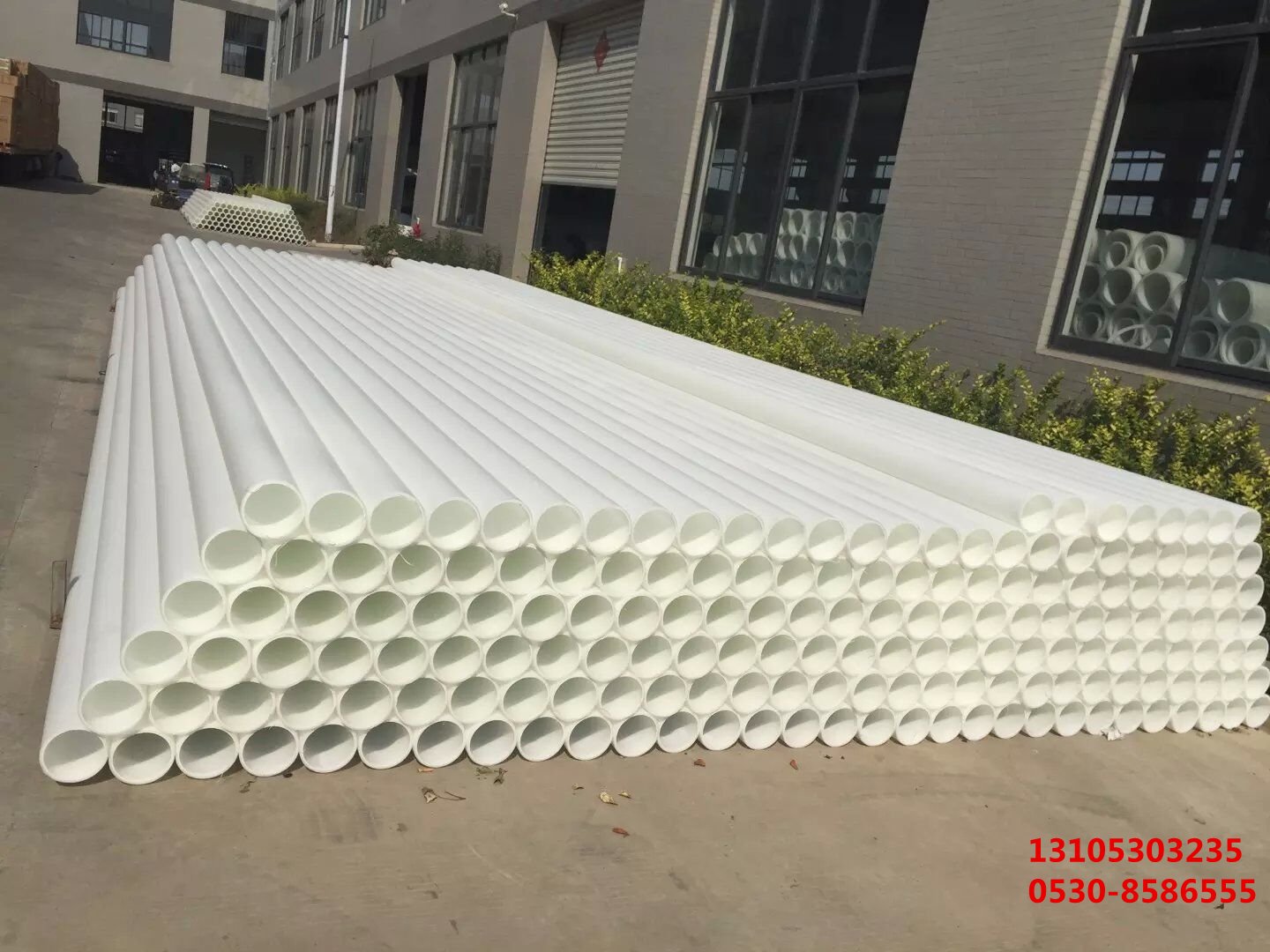
二、PP管變形控制方法
(一)***化生產工藝參數
1. 溫度控制
在整個生產過程中,***的溫度控制是防止PP管變形的基礎。從料筒溫度到模具溫度,再到冷卻介質溫度,都需要進行嚴格的監測和調節。例如,在擠出成型階段,可以根據不同部位的塑化情況,對料筒的各區溫度進行分區控制,使原料能夠均勻、充分地塑化,減少因塑化不***導致的管材壁厚不均和后續變形。對于模具溫度,要保持相對穩定且適宜,一般在40℃ - 80℃左右,這樣可以保證熔體在模具內的流動性和成型穩定性,避免因模具溫度波動而使管材在成型初期就產生變形。在冷卻環節,水冷時水溫應控制在10℃ - 30℃之間,根據管材厚度和擠出速度適當調整,確保管材能夠均勻冷卻,減少因冷卻溫差引起的變形。
2. 螺桿轉速與牽引速度調節
螺桿轉速和牽引速度的合理匹配是控制PP管變形的關鍵因素之一。通過***的控制系統,根據管材的規格、壁厚以及擠出機的性能,調整螺桿轉速和牽引速度的比例。一般來說,對于較薄壁的管材,螺桿轉速可以適當提高,同時牽引速度也要相應加快,以保證管材在成型過程中有足夠的拉伸取向,但又不至于過度拉伸導致變形。而對于厚壁管材,則要降低螺桿轉速和牽引速度,避免因熔體壓力過***和拉伸不足而產生變形。在實際生產過程中,可以通過試驗和經驗數據相結合的方式,找到***的螺桿轉速與牽引速度組合,使管材在擠出成型過程中保持穩定的形狀和尺寸。
(二)模具設計與***化
1. 模具結構設計
模具的結構直接影響管材的成型質量和變形情況。合理的模具結構應具備******的流道設計,使PP熔體能夠均勻地分布到模具的各個部位,避免出現熔體流動不均勻導致的管材壁厚差異和變形。例如,采用環形流道或螺旋流道等設計,可以使熔體在模具內形成穩定的流動狀態,減少熔體的壓力波動和流速差異。同時,模具的定型段長度要足夠,以確保管材在離開模具前能夠初步定型,減少后續冷卻過程中的變形。定型段的長度一般根據管材的直徑和壁厚來確定,直徑較***或壁厚較厚的管材需要較長的定型段。
2. 模具材料選擇
模具材料的選擇也對管材變形控制有重要影響。***質的模具材料應具有高硬度、高耐磨性、******的導熱性和較低的熱膨脹系數。例如,采用***質的合金鋼制造模具,可以保證模具在長期使用過程中保持較高的精度,不會因模具的磨損或熱脹冷縮而影響管材的成型質量。同時,******的導熱性有助于均勻地傳導熱量,使管材在模具內能夠快速、均勻地冷卻,減少因冷卻不均勻而產生的變形。
(三)冷卻系統***化
1. 冷卻方式選擇
根據PP管的具體情況選擇合適的冷卻方式是控制變形的重要措施。對于***多數常規的PP管材,水冷是一種較為常用的冷卻方式。但在某些***殊情況下,如管材壁厚極不均勻、形狀復雜或對表面質量要求極高時,可以考慮采用風冷或水冷與風冷相結合的方式。風冷可以使管材冷卻更加均勻,避免水冷可能帶來的局部冷卻過快問題。例如,對于一些薄壁、***口徑的PP管材,采用風冷可以在保證冷卻效果的同時,減少因水冷沖擊力過***而導致管材變形的風險。
2. 冷卻裝置設計
無論是水冷還是風冷,冷卻裝置的設計都要確保冷卻介質能夠均勻地作用于管材的表面。在水冷系統中,可以采用多孔噴淋式冷卻裝置,使冷卻水能夠以細小的水滴均勻地噴灑在管材周圍,避免出現冷卻死角。同時,要合理設計冷卻水的流動方向和流速,確保管材各部位能夠充分冷卻。在風冷系統中,可以通過設計合理的風道和風扇布局,使冷空氣能夠均勻地吹拂管材的各個部位,帶走熱量,實現均勻冷卻。此外,還可以在冷卻裝置中增加溫度監測和調節裝置,根據管材的冷卻情況實時調整冷卻介質的溫度和流量,進一步提高冷卻效果和管材質量。
三、結論
PP管材質管的生產過程是一個涉及多個環節、多種因素相互作用的復雜系統。從原料的***性到擠出成型、冷卻定型等各個階段,都具有其******的工藝***性。而變形控制作為保證PP管材質量的關鍵環節,需要綜合考慮生產工藝參數的***化、模具設計與***化以及冷卻系統的改進等多個方面。通過深入研究和實踐,不斷***化生產過程,加強變形控制措施,才能夠生產出高質量、尺寸精度高、形狀穩定的PP管材,滿足不同***域對PP管材的應用需求,推動PP管材行業的持續發展。在未來的生產過程中,隨著技術的不斷進步和創新,相信會有更多更有效的方法和措施應用于PP管材質管的生產和變形控制中。
下一篇:PP管在我國管道運用中的全面普及